412
May 28-2024
Design Focus of Warehouse Racking Systems
The design focus of warehouse racking systems mainly lies in the analysis and calculation of the forces acting on the racks.
The design basis is primarily derived from the following aspects:
|
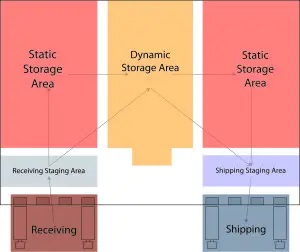
|
1. Live Load:
Live load refers to the weight of the goods and pallets placed on the warehouse racks, and also includes loads from snow or rain on the roof.
2. Dead Load:
Dead load refers to the self-weight of the warehouse racking structure, including the weight of connecting C-shaped steel, trusses, beams, roof panels, and wall panels.
3. Vertical Impact Load:
This refers to the impact load generated when a stacker places goods.
4. Wind Load:
Wind load is a crucial factor in the force calculations for an integrated warehouse. Generally, the investors in integrated warehouses aim to utilize space effectively, which results in taller warehouses. The height-to-width ratio typically ranges from 1 (height) to 1.5-2W (width). Therefore, the safety of the warehouse under wind load is a critical metric. Calculating the impact of wind load on the warehouse racking columns is usually done using steel structure force calculation software, supplemented by system force simulation and theoretical calculations for verification.
5. Seismic Load:
Seismic load is calculated according to GBJ11-89 "Code for Seismic Design of Buildings", with a typical seismic fortification intensity of 7 degrees.
High-rise racking technology has been widely mastered, and many patents have been obtained. The production of key components has been fully localized. However, in terms of control technology-based information technology, there is still a gap compared to Western developed countries. Meanwhile, the rapidly growing logistics market in China has attracted some international companies to enter the market swiftly.
Automated Storage and Retrieval Systems (AS/RS) in China
Automated storage and retrieval systems have gained widespread recognition in China. This system, which has emerged in recent years, is a crucial component of modern logistics systems. Using AS/RS not only saves space but also increases warehouse capacity. With the integration of computers, electronic information, photoelectric technology, and mechanical automatic control into a new control system, all goods receiving and dispatching tasks are completed by computers. Managers only need to input the relevant instructions to complete all processes, thus realizing automated control of the storage process and significantly improving logistics efficiency.
As information technology improves, some domestic warehouse enterprises have adopted a dual approach: absorbing advanced foreign technology while focusing on self-development and increasing R&D efforts. This has led to breakthrough developments in AS/RS technology, with the design and development of various hardware and software products for automated systems. High-rise racking and information control technology are two fundamental aspects of automated storage systems. Throughout the development of AS/RS, innovations such as different types of inventory management software, system simulation software, graphical monitoring and scheduling software, stacker conveyor control software, barcode recognition and tracking systems, and handling robots have generated significant social and economic benefits.
Functions and Roles of Warehouse Racking Systems
Quality Assurance:
Racking systems ensure the quality of stored goods by implementing measures such as moisture-proofing, dust-proofing, theft prevention, and damage protection, thereby enhancing the quality of material storage. Mechanization and Automation: Many new racking structures and functionalities are conducive to the mechanization and automation of warehouse management.
-
Space Utilization: Racking systems are structured frameworks that maximize warehouse space utilization, enhancing storage capacity.
-
Damage Reduction: Goods stored on racks are not compressed against each other, reducing material loss and ensuring the integrity of the goods, thereby minimizing damage.
-
Convenient Access: Goods stored on racks are easily accessible, facilitating inventory counting and management, and enabling first-in, first-out (FIFO) practices.
-
Quality Assurance: Racking systems ensure the quality of stored goods by implementing measures such as moisture-proofing, dust-proofing, theft prevention, and damage protection, thereby enhancing the quality of material storage.
-
Mechanization and Automation: Many new racking structures and functionalities are conducive to the mechanization and automation of warehouse management.

Prev
Next
